Top 10 Equipment Issues Faced by Kitchen Managers
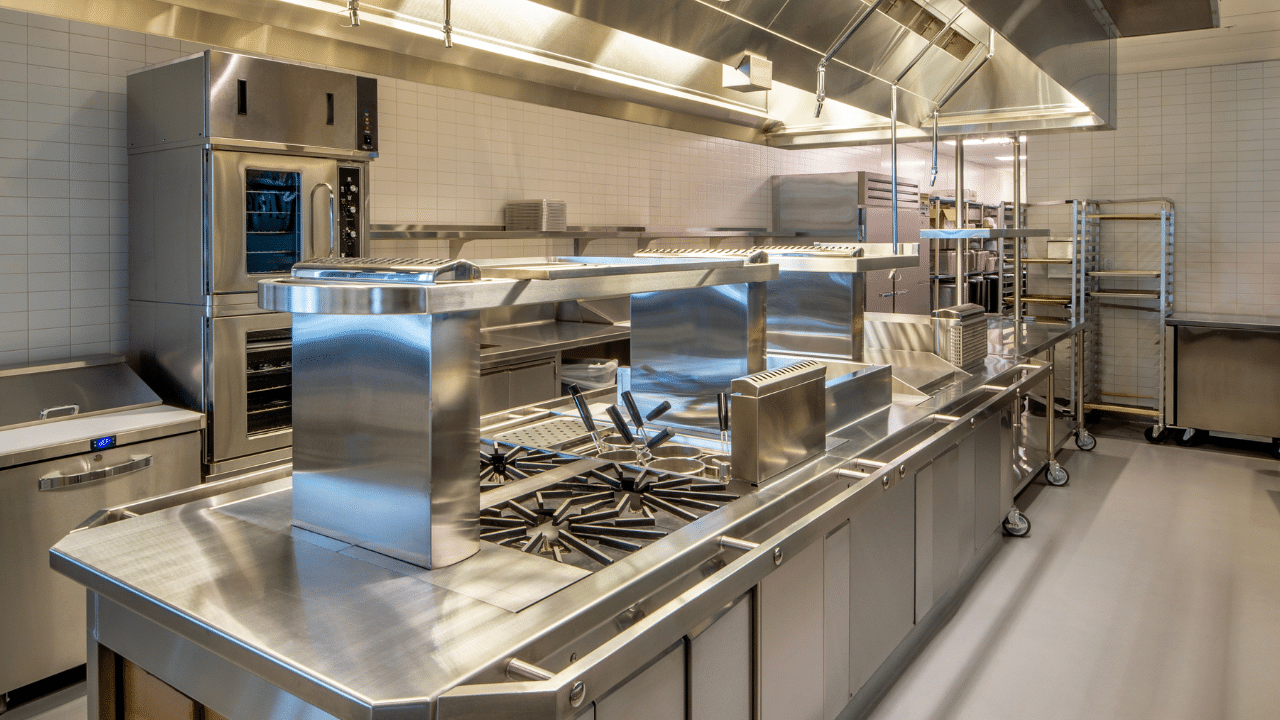
Maintaining a productive and efficient commercial kitchen involves more than skilled staff and great recipes. It requires reliable equipment to keep operations running smoothly. In this guide, we’ll explore the top equipment issues kitchen managers face and how they can impact food quality, safety, and service. From refrigeration failures to burner ignition problems, knowing how to address these challenges is key to minimizing disruptions and maintaining a high-performing kitchen.
Are you ready to keep your kitchen running efficiently and avoid costly breakdowns? Discover how Smart Care’s expert maintenance and repair services can support your operations.
Common Commercial Kitchen Equipment Issues and Solutions
1. Refrigeration Failures:
Fluctuating temperatures in refrigerators and freezers can lead to significant food spoilage and health code violations. Common culprits include dirty condenser coils that reduce cooling efficiency, worn or faulty door seals that let cold air escape, and failing compressors.
Solution: Scheduling routine servicing ensures that coils are cleaned, seals are inspected, and compressors are tested for proper function. A professional technician from Smart Care can detect minor issues before they lead to costly repairs or breakdowns.
2. Oven Inconsistencies:
Uneven heating in ovens can cause undercooked or overcooked food, affecting the consistency and quality of menu items. This issue often arises due to faulty heating elements, calibration problems, or worn-out thermostats.
Solution: Regular oven inspections and calibrations help maintain accurate temperatures and efficient heating. Technicians can replace worn components and ensure proper airflow, preventing heat distribution problems.
3. Dishwasher Malfunctions:
Commercial dishwashers are essential for maintaining hygiene and cleanliness. Common problems include poor water drainage, leaks, and ineffective cleaning cycles caused by clogged filters, damaged hoses, or malfunctioning spray arms.
Solution: Routine maintenance includes inspecting spray arms, clearing filters, and checking for leaks. Preventative servicing ensures optimal cleaning performance and avoids health code violations due to unclean dishware.
4. Ventilation System Failures:
Inadequate ventilation can create a stuffy, overheated kitchen environment and cause equipment to overheat. Grease buildup in ducts and filters is a frequent cause of ventilation issues and fire hazards.
Solution: Regularly scheduled cleaning of ducts, hoods, and filters removes grease buildup and ensures proper airflow. Technicians can also inspect fans and motors for wear to keep the system operating efficiently.
5. Deep Fryer Breakdowns:
Deep fryers are prone to grease accumulation, which can clog components, cause uneven heating, and increase the risk of fires. Lack of maintenance can lead to faulty thermostats and heating element failures.
Solution: Preventative servicing includes draining and cleaning fryers, inspecting thermostats, and ensuring heating elements are in good condition. Scheduled servicing reduces the risk of grease-related fires and extends the fryer’s life.
6. Burner Ignition Problems:
Gas stove burners that fail to ignite disrupt kitchen workflows, leading to delays during peak service hours. This issue often stems from clogged gas lines, faulty ignition switches, or dirty pilot lights.
Solution: Regular servicing involves cleaning burner components, inspecting gas lines, and replacing defective igniters. Maintenance ensures that burners ignite reliably, minimizing downtime in the kitchen.
7. Ice Machine Blockages:
Mineral deposits and clogged water filters in ice machines can obstruct water flow and prevent ice production, affecting beverage service and customer satisfaction.
Solution: Scheduled maintenance includes descaling to remove mineral buildup, cleaning filters, and inspecting the water line. Consistent servicing helps prevent blockages and keeps ice production running smoothly.
8. Equipment Overheating:
Kitchen equipment like ovens, fryers, and griddles can overheat due to dirty filters, blocked vents, or malfunctioning thermostats. Overheating damages the equipment and poses a safety risk.
Solution: Regular air vents, filters, and thermostat inspections prevent airflow obstructions and overheating. Servicing also ensures that cooling fans and components function correctly.
9. Leaking Appliances:
Leaks in dishwashers, refrigerators, and sinks can lead to water damage, slippery floors, and unsafe working conditions. Damaged seals, cracked hoses, or loose connections are common causes.
Solution: Preventative maintenance involves inspecting and replacing seals, tightening connections, and repairing damaged hoses to prevent costly water damage and safety hazards.
10. Electrical Issues:
Frequent circuit breaker tripping, flickering lights, and sudden equipment shutdowns often indicate overloaded circuits or faulty wiring. These electrical problems can disrupt operations and pose a safety risk.
Solution: Scheduling electrical inspections ensures that wiring, outlets, and circuit breakers are in good condition. Technicians can identify overloaded circuits and suggest upgrades to handle the kitchen’s power demand.
Why Preventative Maintenance Matters
By scheduling regular maintenance checks, kitchen managers can avoid unexpected breakdowns, reduce repair costs, and extend the lifespan of their equipment. Preventative servicing helps maintain a safe, efficient working environment and ensures that kitchen operations run smoothly. For comprehensive maintenance solutions, Smart Care provides expert support tailored to your kitchen’s needs.
Keep Your Kitchen Equipment Running Smoothly with Smart Care Solutions
Commercial kitchens thrive on reliable, well-maintained equipment. Scheduled maintenance can address common issues like refrigeration failures, burner ignition problems, and ventilation inefficiencies, preventing costly breakdowns and extending the lifespan of your equipment. Contact Smart Care at (888)-887-1675 for more information, or fill out our contact form. Our services are available nationwide. Visit our Find Service Page to locate a service technician near you. Don’t wait until an issue disrupts your kitchen. Partner with Smart Care and maintain peak performance today!