Commercial Ice Machine Maintenance & Repair Tips
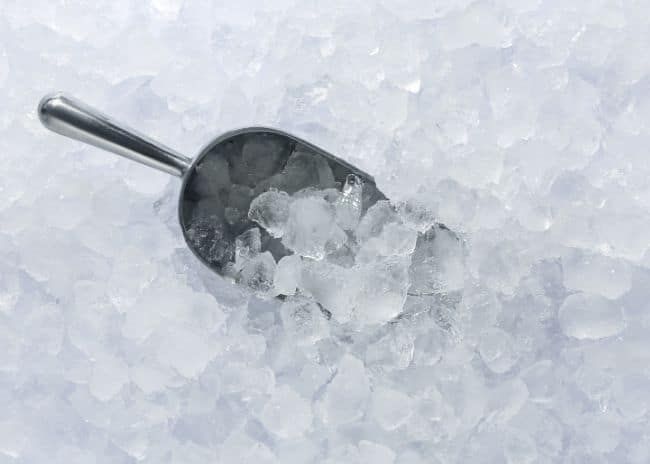
Maintaining your commercial ice machine is vital for keeping it in top shape and avoiding costly repairs. It’s important to make sure it’s properly cleaned, ventilated, managed and maintained.
Nobody wants the costly repairs and customer displeasure that can come with an out-of-service ice machine. In order to avoid repairs from being needed in the first place, you have to make sure your ice machine is properly cleaned, ventilated, managed and maintained.
The easiest way to do that? By checking out the following commercial ice machine maintenance tips.
What is the most important part of proper ice machine maintenance?
The most important part of proper ice machine maintenance is staying on top of regular cleaning and sanitation. These practices help keep the ice that’s produced as high-quality as possible, avoiding downtime-inducing leaks and clogs. Here are some commercial ice machine maintenance tips you can use to keep performance at its peak:
- Make sure airflow isn’t blocked. Ensure that the ice machine has proper ventilation and airflow. Adequate ventilation helps prevent the buildup of heat and dust, which can affect the machine’s efficiency.
- Keep the ice bin and maker clean. Regularly remove any ice from the bin and clean it with a mild detergent and warm water before a thorough rinse. Follow the manufacturer’s instructions to clean the internal components of the ice maker — typically, it involves removing and cleaning internal components.
- Sanitize every time you clean. After cleaning, it’s essential to sanitize the machine. You can use a commercial ice machine sanitizer or a mixture of water and food-grade sanitizer. Make sure to rinse thoroughly afterward.
- Stay on top of changing filters. If your ice machine has a water filter, change it as recommended by the manufacturer to ensure the ice remains clean and clear.
- Conduct regular inspections. Regularly inspect the machine for any signs of wear or damage, such as worn gaskets or loose connections. Replace any faulty parts promptly.
- Schedule planned maintenance. Scheduling regular planned maintenance will help you avoid small issues turning into far bigger, downtime-causing ones.
How much does it cost to repair a commercial ice machine?
The exact cost of repairing a commercial ice machine will vary quite a bit depending on the type and extent of the issue alongside the age and brand of the machine. Having your valves, gaskets, seals or evaporator plates replaced — especially on recent models — tends to be straightforward in both price and practice. Older machines and machines with unique or out-of-stock parts cost more to repair just like more complex issues like refrigerant leaks do.
Why won’t my commercial ice machine dispense ice?
If your commercial ice machine isn’t dispensing ice, there are a number of potential causes you can inspect for:
- Power: Ensure it’s plugged in and has power. Check the circuit breaker and fuses.
- Water Supply: Verify the water supply is working and the valve is open.
- Bin Full Sensor: Check for a full ice bin or malfunctioning sensors.
- Ice Blockages: Clear any ice blockages in the dispenser area.
- Cleanliness: Make sure the ice bin and dispenser are clean.
- Temperature: Ensure the machine is within the correct temperature range.
- Water Filtration: Check and replace any clogged water filters.
- Error Codes: Look for error codes on the display and consult the manual for guidance.
What should I do if I need assistance with my commercial ice machine?
Want to know a secret? We have one major commercial ice machine maintenance tip we haven’t told you yet: Always have an emergency repair service provider on speed dial. Because even when you try your best, sometimes things break down. When they do, you don’t want to increase your downtime even further by having to vet a bunch of companies before finding the right one.
Smart Care technicians are available 24/7/365 to answer your repair and maintenance calls — even when they’re about ice machines.